1.
Deposizione chimica da vapore (CVD): I gas di partenza del carbonio tipicamente utilizzati includono idrocarburi come etilene e metano, mentre per il catalizzatore si scelgono solitamente catalizzatori metallici come ferro, nichel, cobalto, ecc. Il substrato da depositare (ad esempio, wafer di silicio, wafer di vetro, ecc.) viene collocato in una camera di reazione per garantire che la superficie del substrato sia pulita e piatta. La camera di reazione viene riscaldata a una temperatura adeguata e quindi estratta a un certo livello di vuoto per garantire la purezza e la stabilità dei gas durante il processo di reazione. Il gas sorgente di carbonio e il gas catalizzatore vengono introdotti nella camera di reazione attraverso un sistema di alimentazione del gas per controllare la portata e il volume del gas. Il gas di partenza del carbonio si dissocia sulla superficie del catalizzatore per generare atomi di carbonio, che vengono successivamente depositati sulla superficie del substrato per formare nanotubi di carbonio. Il tempo di crescita dei nanotubi di carbonio è controllato, di solito da minuti a ore, per controllare la lunghezza e la densità dei nanotubi. Una crescita prolungata produce nanotubi di carbonio più lunghi e più densi. Al termine della crescita, l'alimentazione della fonte di carbonio e del gas catalizzatore viene interrotta e la camera di reazione viene raffreddata a temperatura ambiente. Al termine della reazione, il gas residuo nella camera di reazione viene rimosso fornendo un gas inerte come azoto o argon.
2. Metodo di rivestimento: La sospensione di nanotubi di carbonio viene rivestita sulla superficie del substrato mediante spin-coating, spruzzatura, spazzolatura o laminazione. Durante il processo di rivestimento, è possibile controllare parametri quali la velocità di rivestimento e la velocità di rotazione della testa di rivestimento per controllare lo spessore e l'uniformità del film. Dopo la verniciatura, il rivestimento viene posto in un'area ventilata o su un banco riscaldato per indurre l'evaporazione del solvente. Dopo la completa evaporazione del solvente, si procede all'essiccazione per formare un film uniforme di nanotubi di carbonio. Opzionalmente, il film di nanotubi di carbonio viene trattato termicamente per migliorarne la cristallinità e le proprietà meccaniche. Le condizioni di trattamento termico possono essere regolate a seconda delle necessità e sono solitamente eseguite in atmosfera di gas inerte.
3. Filtrazione: I materiali delle membrane filtranti comunemente utilizzati includono membrane in policarbonato (PC), poliestere (PET) e poliammide (Nylon), mentre la dimensione dei pori viene solitamente selezionata in base allo spessore del film e alla permeabilità desiderati. La sospensione di nanotubi di carbonio viene filtrata sulla membrana filtrante mediante vuoto o pressione. Le operazioni di filtrazione possono essere eseguite utilizzando apparecchiature come imbuti di filtrazione sotto vuoto o filtri a membrana.
4. Metodo di strippaggio: i metodi di strippaggio più comuni includono lo strippaggio meccanico, in cui la pellicola di nanotubi di carbonio viene direttamente strippata dal substrato utilizzando strumenti di strippaggio (ad es, nastri, raschietti, ecc.); stripping chimico, in cui il film di nanotubi di carbonio cresciuto viene posto in un solvente o in una soluzione appropriata in modo da danneggiare il legame tra il film e il substrato per realizzare lo stripping; e stripping termico, in cui il substrato o il film viene riscaldato per farlo espandere o contrarre termicamente per distruggere il legame tra il substrato e il film per realizzare lo stripping; e stripping termico, in cui il substrato o il film viene riscaldato per farlo espandere o contrarre termicamente per distruggere il legame tra il substrato e il film per realizzare lo stripping. e la pellicola riscaldando il substrato o la pellicola, facendoli espandere e contrarre termicamente, rompendo così il legame tra il substrato e la pellicola.
5.3.3 Caso di studio: Membrane a osmosi inversa potenziate con nanotubi di carbonio
Un'applicazione unica dei nanotubi di carbonio, oltre alle applicazioni funzionali simili ad altri tipi di membrane di filtrazione, sono le membrane a osmosi inversa. Questa tecnologia di separazione a membrana è in grado di separare dall'acqua impurità, ioni, microrganismi, ecc. ed è ampiamente utilizzata nei settori dell'acqua potabile, del trattamento delle acque reflue industriali e della desalinizzazione dell'acqua marina. Tuttavia, la membrana ad osmosi inversa presenta il problema del basso flusso e della scarsa efficienza di trattamento. Per risolvere questo problema, gli studiosi hanno introdotto i nanotubi di carbonio nelle membrane a osmosi inversa. I nanotubi di carbonio hanno proprietà eccellenti come l'elevata area superficiale specifica, l'alta resistenza, l'alta conducibilità, ecc. che possono formare una sorta di canale conduttore di protoni nella membrana a osmosi inversa e aumentare il flusso. Allo stesso tempo, i nanotubi di carbonio possono anche adsorbire ioni, microrganismi e altre impurità presenti nell'acqua, migliorando efficacemente l'efficienza di purificazione dell'acqua e la durata della membrana a osmosi inversa. Attualmente, la membrana a osmosi inversa basata sui nanotubi di carbonio è stata introdotta nell'uso commerciale, nel campo dell'acqua potabile, della desalinizzazione dell'acqua di mare e in altri settori per ottenere risultati significativi. In futuro, la ricerca e la tecnologia di preparazione dei materiali a base di nanotubi di carbonio saranno ulteriormente sviluppate e il flusso e l'efficienza di lavorazione delle membrane a osmosi inversa saranno costantemente migliorati.
Tabella 2 Confronto tra le proprietà dei nanotubi di TiO2, GO e CNT
Proprietà
|
Membrane a nanotubi di biossido di titanio (TiO2)
|
Membrane di ossido di grafene (GO)
|
Membrane di nanotubi di carbonio (CNT)
|
Struttura del materiale
|
Nanotubi di ossido di titanio
|
Ossido di grafene con gruppi funzionali contenenti ossigeno
|
Nanotubi di carbonio
|
Metodo di preparazione
|
Metodo di soluzione Metodo di deposizione da vapore Metodo elettrochimico
|
Metodo di rivestimento Metodo di deposizione chimica da vapore Metodo idrotermico
|
Metodo di deposizione chimica da vapore Metodo di rivestimento Metodo di filtrazione
|
Aree di applicazione
|
Fotocatalisi Dispositivi fotovoltaici Purificazione dell'acqua e dell'aria
|
Trattamento dell'acqua Purificazione dell'aria Separazione molecolare Biomedicina
|
Trattamento dell'acqua Membrane ad osmosi inversa Separazione molecolare Biomedicina
|
Vantaggi
|
Elevata area superficiale Speciali proprietà fotovoltaiche Attività fotocatalitica
|
Molti gruppi funzionali contenenti ossigeno Elevata attività superficiale Selettività molecolare
|
Elevata resistenza Elevata conducibilità Elevata area superficiale specifica Prestazioni regolabili
|
Svantaggi
|
Processo di preparazione complesso e costo elevato
|
Incline a difetti strutturali e scarsa stabilità durante il processo di preparazione
|
Processo di preparazione complesso Elevati requisiti di controllo del processo
|
Applicazioni
|
Trattamento fotocatalitico dell'acqua Purificazione dell'aria Preparazione di dispositivi fotovoltaici
|
Trattamento dell'acqua Separazione molecolare Applicazioni biomediche
|
Membrane a osmosi inversa Separazione molecolare Applicazioni biomediche
|
6 Membrane basate su strutture organiche metalliche (MOF)
6.1 Che cosa sono le membrane MOF
Il
Metal Organic Framework (MOF) è un polimero di coordinazione realizzato mediante l'autoassemblaggio di ligandi organici polidentati contenenti ossigeno, azoto, ecc. con ioni di metalli di transizione. È costituito da centri metallici inorganici e ligandi organici a ponte collegati tramite autoassemblaggio per formare un materiale cristallino poroso con una struttura a rete periodica. In quanto materiale ibrido organico-inorganico, il MOF possiede sia la rigidità dei materiali inorganici che la flessibilità dei materiali organici.
Le strutture a spina dorsale in diverse dimensioni sono determinate principalmente dalla coordinazione tra ligandi organici e ioni metallici e dal legame a idrogeno. Durante il processo di sintesi, i reagenti residui e le piccole molecole di solventi occupano i pori della struttura a scheletro, mentre la rimozione delle piccole molecole mediante trattamento di attivazione può lasciare una struttura di pori persistente. Le dimensioni e la struttura dei pori possono essere modificate cambiando la struttura dei ligandi organici e il tipo di ioni metallici nel materiale sintetizzato, per controllare l'area superficiale specifica e la porosità in base alle diverse applicazioni. Attualmente, i materiali a scheletro metallo-organico utilizzati insieme a ligandi neutri organici eterociclici contenenti azoto o a ligandi anionici organici contenenti carbossile possono essere sintetizzati in grandi quantità, il che rappresenta un grande potenziale per lo sviluppo e l'applicazione nella moderna ricerca sui materiali.
6.2 Come produrre membrane MOF
1. Metodo di sintesi in situ: in base alle particolari proprietà superficiali del supporto stesso, il supporto viene inserito direttamente nel sistema di sintesi e, in determinate condizioni, la superficie del supporto e la notte di formazione del film entrano direttamente in contatto e quindi reagiscono, per preparare una membrana continua. Il metodo di sintesi in situ è semplice e facile da utilizzare, facile da realizzare su larga scala, ma è difficile preparare membrane MOF continue, perché le proprietà chimiche tra i materiali MOF e i carrier sono più diverse, il tasso di nucleazione dei cristalli è ridotto, con conseguente bassa densità di nucleazione eterogenea dei cristalli MOF sulla superficie del carrier e scarso legame tra la membrana e il carrier.
2. Metodo di crescita secondaria del seme di cristallo: utilizzare innanzitutto il metodo idrotermale per far crescere il seme di cristallo sul substrato, quindi, dopo il processo di nucleazione del cristallo, la crescita dello strato di membrana, la crescita secondaria del materiale per ottenere una membrana densa. Infine, le specie cristalline della superficie del substrato poroso dopo l'alta temperatura, la reazione di condensazione tra i gruppi e i grani di zeolite combinati per formare legami covalenti. Tuttavia, il metodo è in qualche modo limitato perché la membrana filtrante non resiste alle alte temperature.
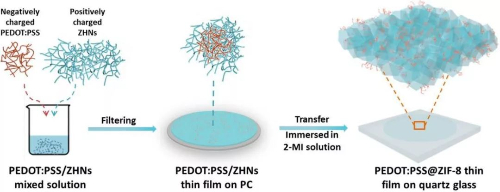
Fig. 10 Sintesi schematica di un film MOF: Film PSS@ZIF-8
6.3 Applicazione specializzata nella rimozione dei metalli pesanti
Oltre alle applicazioni funzionali simili ad altri tipi di membrane filtranti, le membrane MOF possono essere applicate al trattamento degli ioni di metalli pesanti. Le membrane MOF hanno una struttura porosa altamente ordinata formata da ioni metallici e ligandi organici attraverso il legame chimico dei ligandi. Questa struttura porosa ha un diametro e una dimensione dei pori regolabili, fornendo molti siti e canali di adsorbimento, favorevoli all'adsorbimento e all'incorporazione di ioni di metalli pesanti. Ciò consente di utilizzare i film MOF nel campo del trattamento delle acque, ad esempio per la rimozione di ioni metallici pesanti inquinanti, come piombo, cadmio e mercurio, dalle acque sotterranee, dalle acque reflue industriali e dalle acque reflue municipali. Le dimensioni altamente controllabili dei pori e la funzionalizzazione della superficie dei film MOF consentono un efficiente adsorbimento e la separazione selettiva di specifici ioni di metalli pesanti. Svolgono inoltre un ruolo nel trattamento di adsorbimento e recupero per la bonifica ambientale e i processi di trattamento delle acque reflue. I film MOF possono realizzare un'efficiente cattura e recupero dei metalli target durante l'adsorbimento degli ioni di metalli pesanti. Attraverso adeguati metodi di post-trattamento, gli ioni di metalli pesanti adsorbiti possono essere desorbiti dal film MOF, realizzando un efficace recupero e riutilizzo delle risorse metalliche.
7 Membrana filtrante composita
Le membrane filtranti composite sono diverse dalle tradizionali membrane filtranti monomateriale in quanto combinano due o più materiali per sfruttare appieno i rispettivi punti di forza e compensare le rispettive carenze, ottenendo così una filtrazione più efficiente e affidabile. Questi materiali possono essere polimeri, ceramiche, metalli, nanomateriali, ecc. Ogni materiale ha proprietà fisiche, chimiche e meccaniche uniche e può essere combinato in modo flessibile in base ai diversi requisiti di filtrazione.
Nelle batterie agli ioni di litio, una membrana composita PVDF-MOF con uno strato continuo di MOF funge da diaframma ad alte prestazioni. La struttura uniforme dei pori e i canali subnano con siti metallici aperti collegati nello strato MOF continuo possono generare un flusso di Li+ uniformemente distribuito, inibire la formazione di protrusioni dendritiche e migliorare le prestazioni elettrochimiche.
Fig. 11 Separatore composito PVDF-MOF con strato continuo di MOF [5]
Nel campo della desalinizzazione dell'acqua di mare, la distillazione a membrana (MD) è emersa come una strategia alternativa di desalinizzazione dell'acqua di mare in grado di ridurre ampiamente i costi di capitale e il consumo energetico. Nel processo MD, quasi il 100% dei componenti non volatili viene rimosso e non vi è alcuna limitazione sulla concentrazione dell'acqua di alimentazione, mentre il processo di osmosi inversa a pressione (RO) ha un potenziale minore per il trattamento di soluzioni ad alta salinità con un basso recupero di acqua. I componenti volatili vengono separati dalla miscela di alimentazione utilizzando una membrana idrofobica microporosa e il sistema funziona al di sotto del punto di ebollizione del liquido di alimentazione. Per le applicazioni MD, spesso si preferiscono materiali polimerici con bassa energia superficiale, elevata stabilità termica, chimica e inerzia. Il politetrafluoroetilene (PTFE) e il fluoruro di polivinilidene (PVDF) sono considerati i principali materiali di membrana disponibili in commercio per la distillazione a membrana sotto vuoto (VMD), grazie alla loro elevata stabilità termica e idrofobicità. Il PVDF e il PTFE sono i polimeri ottimali per le applicazioni VMD grazie alla loro eccellente resistenza chimica e durata. Queste proprietà consentono al PVDF di resistere agli ambienti chimici aggressivi che spesso si incontrano nei sistemi VMD, garantendo un'affidabilità operativa a lungo termine. Il PTFE, invece, svolge un ruolo fondamentale grazie alle sue proprietà antiaderenti e all'eccellente resistenza alle alte temperature. Nei sistemi VMD, il PTFE contribuisce a migliorare le prestazioni della membrana e previene efficacemente le incrostazioni, assicurando così un trasporto efficiente e senza ostacoli del vapore attraverso la membrana durante la distillazione. Nelle applicazioni VMD, l'uso sinergico di PVDF e PTFE migliora la durata, la resistenza chimica e l'efficienza operativa dell'intero sistema di membrane.
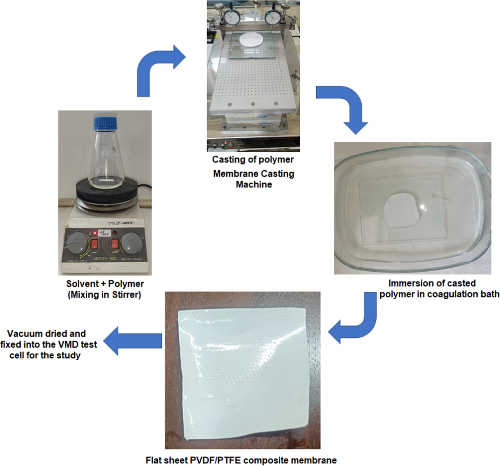
Fig. 12 Diagramma di flusso sulla preparazione della membrana composita microporosa PVDF-PTFE [6]
8 Conclusioni
Le membrane filtranti realizzate con diversi materiali sono utilizzate in diversi campi grazie alle loro diverse caratteristiche e possono essere selezionate in base a diverse esigenze oltre al processo di filtrazione di base. Le membrane in PVDF possono essere utilizzate per filtrare microrganismi come i batteri e per la purificazione dei materiali nella produzione chimica; le membrane in ceramica sono utilizzate soprattutto nell'industria alimentare per la separazione delle bevande alcoliche; le membrane in nanotubi di biossido di titanio possono essere utilizzate per applicazioni correlate e per il trattamento degli ioni di metalli pesanti grazie alle loro proprietà fotocatalitiche; le membrane di ossido di grafene possono essere utilizzate per la separazione molecolare, oltre che per la desalinizzazione dell'acqua di mare e la separazione di olio e acqua; i nanotubi di carbonio possono essere utilizzati come membrane per l'osmosi inversa; le membrane MOF possono essere utilizzate per separare selettivamente gli ioni di metalli pesanti grazie alla natura dei composti di coordinazione. Inoltre, in base alle esigenze dei diversi scenari applicativi, è possibile utilizzare diversi tipi di membrane di filtrazione in combinazione tra loro, e il tipo di membrana composita può ottenere un migliore effetto di filtrazione integrando le caratteristiche di diversi tipi di membrane di filtrazione materiali.
Stanford Advanced Materials (SAM) non solo è in grado di fornire un'ampia gamma di prodotti a membrana di filtrazione, ma anche di offrire una consulenza professionale per la scelta, che potrete
consultare immediatamente.
Lettura correlata:
Riferimenti:
[1] Khayet M, Feng C, Khulbe K, et al. Preparazione e caratterizzazione di membrane a fibra cava di fluoruro di polivinilidene per l'ultrafiltrazione[J]. Polymer, 2002, 43(14).
[2] Li M, Cheng S, Zhang J, et al. Membrane composite a base di poli(fluoruro di vinilidene) con strato continuo di struttura metallorganica per separatori ad alte prestazioni di batterie agli ioni di litio[J]. Chemical Engineering Journal, 2024, 487.
[3] Hu W, Zhang F, Tan X, et al. Fabbricazione di film compositi antibatterici PVDF a struttura gerarchica simile a corallo per l'effetto di autopulizia e raffreddamento radiativo[J]. ACS applied materials & interfaces, 2024.
[4] Wei Y, Li K, Li P, et al. Miglioramento della filtrazione delle membrane ceramiche mediante pre-ossidazione PS con catalisi FeSO4 assistita da CuO per la rimozione di NOM nel trattamento dell'acqua potabile[J]. Separation and Purification Technology,2024,345.
[5] Membrane ceramiche e loro applicazione nel trattamento di alimenti e bevande[J]. Filtrazione e separazione, 2000, 37(3).
[6] Mala M M ,S. S ,S. F , et al. Desalinizzazione dell'acqua marina e salmastra attraverso una nuova membrana idrofobica composita PVDF-PTFE mediante distillazione a membrana sotto vuoto[J]. Discover Chemical Engineering, 2024, 4(1).